In petrochemical plants, equipment like piping, vessels, and heat exchangers operate under harsh conditions that slowly degrade their integrity. Without early detection, these issues can lead to unplanned shutdowns, environmental risk, and massive repair costs.
Based on API 571, here are five of the most critical damage mechanisms affecting fixed equipment — and how to detect and manage them early using modern tools like RBLX™.
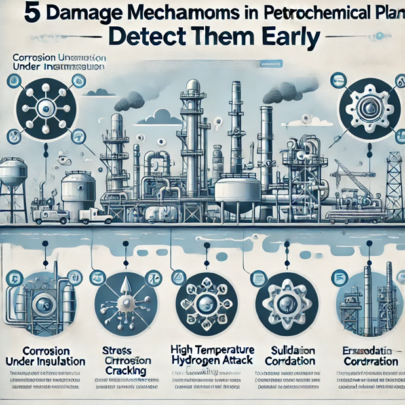
5 Critical Damage Mechanisms in Petrochemical Plants
🔹 1. Corrosion Under Insulation (CUI)
What it is:
CUI occurs when water penetrates damaged insulation and causes corrosion on the metal surface underneath. It’s often hidden and one of the most underestimated threats.
Where it happens:
- Carbon steel and low-alloy steel piping
- Operating between 50°C and 175°C
- Outdoor piping, steam-traced lines, or areas with degraded insulation
How to detect it early:
- Identify CUI-prone assets in RBLX-RBI
- Use guided wave UT, visual inspection, or profile RT
- Track corrosion history and inspection intervals in RBLX-IDMS
- Define CUI Integrity Operating Windows (IOWs) for moisture/temperature control
🔹 2. Stress Corrosion Cracking (SCC)
What it is:
SCC is cracking that occurs due to a specific corrosive environment and tensile stress. It’s often difficult to detect until it leads to failure.
Common types:
- Chloride SCC in stainless steels
- Caustic SCC in carbon steel exposed to caustic solutions
Where it happens:
- Heat exchanger tubes
- Caustic or amine service lines
- Welded zones without proper post-weld heat treatment (PWHT)
How to detect it early:
- Flag SCC risks in RBLX™ based on service and material
- Use TOFD, PAUT, or WFMT for early-stage detection
- Schedule focused inspections using RBI logic
- Keep SCC service history and material stress logs updated in RBLX-IDMS
🔹 3. High Temperature Hydrogen Attack (HTHA)
What it is:
HTHA is a form of degradation that occurs when hydrogen at high temperatures diffuses into steel and reacts with carbides, causing internal damage.
At-risk range:
Above 400°C (750°F) in high-pressure hydrogen environments
Where it happens:
- Hydrogen reformers
- Hydrotreaters
- Reactors in hydrogen-rich service
How to detect it early:
- Use RBLX to evaluate risk zones based on material, temperature, and hydrogen exposure
- Apply Advanced Ultrasonic Backscatter (AUBT) and replica testing
- Conduct fitness-for-service evaluations with RBLX and FITest-FFS™
🔹 4. Sulfidation (Sulfidic Corrosion)
What it is:
Sulfidation happens when sulfur compounds in process streams react with metal surfaces, forming sulfides that weaken the structure.
Risk zone:
Between 260°C and 540°C (500°F to 1000°F)
Where it happens:
- Furnace tubes
- Transfer lines
- Crude and vacuum distillation units
How to detect it early:
- Identify low-silicon carbon steels in service using RBLX material database
- Monitor corrosion rates through UT scans
- Plan targeted inspections using RBLX-RBI based on sulfur exposure
- Log findings in RBLX-IDMS for long-term monitoring
🔹 5. Erosion-Corrosion
What it is:
A combined effect of mechanical wear and corrosion, caused by high-velocity or turbulent flow — especially when carrying solids or vapor-liquid mixtures.
Where it happens:
- Elbows, reducers, and tees
- Pump impellers
- Two-phase flow piping and slurry lines
How to detect it early:
- Model erosion risk zones in RBLX pipeline/piping module
- Monitor flow data and turbulence points
- Use UT mapping or profile RT
- Track wall loss trends and corrective actions in RBLX-IDMS
💡 Smarter Damage Management with RBLX™
RBLX™ software supports proactive risk management by aligning with API 571, API 580, and API 581. It enables engineers and inspectors to:
- Identify damage mechanisms per material and environment
- Assign inspection methods (UT, TOFD, PAUT, RT, etc.)
- Automate inspection planning based on risk
- Track corrosion rates, inspection results, and IOWs
- Integrate with CMMS, FITest-FFS, and field tools
✅ Take Action Before Damage Happens
These mechanisms are predictable and preventable. With the right RBI tools, your team can move from reactive inspections to strategic, cost-saving decisions.
📩 Want to see how RBLX™ can help your facility?
👉 Request a demo at lteng.co.uk/contact or email info@lteng.co.uk
🔑 Keywords for SEO:
- API 571 Damage Mechanisms
- Corrosion Under Insulation (CUI)
- Stress Corrosion Cracking (SCC)
- Sulfidation in Carbon Steel
- Erosion-Corrosion Prevention
- High Temperature Hydrogen Attack Detection
- RBI Software for Petrochemical Plants
- Asset Integrity Management Software
- Inspection Data Management System (IDMS)